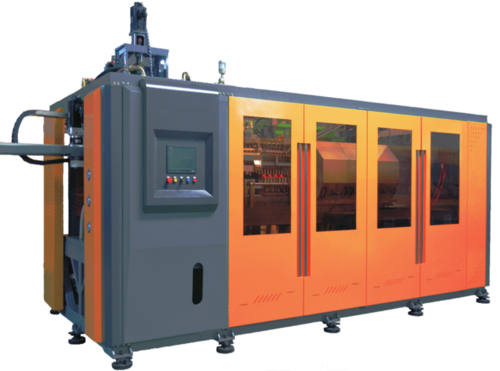
High Speed Blow Molding Machine
80000-150000USD
It is widely used in beverage, edible oil, alcohol and household products like detergent wash liquid.
Full electrical series blowing machine focus on the high speed blowing machine with 4 cavity, 6 cavity, 8 cavity and 9 cavity ranging from 7000BPH to 18000BPH.
1. all electric & electronically servo-controlled, more precise and stable
2. reduce 90% pressure air compress with lower power consumption
3. oil Free / Self Lubricated Bushing Technology.
4. shortest mold change-over time period within 20 minutes.
5. Mitsubishi Make PLC & HMI Display with high performance supporting more than 100 recipes
6. automatic Bottle Ejection system,
7. automatic detect system for temperature and pressure to reduce preforms wastage
Preform inlet unit:
Firstly, the quality preforms are elevated and unscrambled by the auxiliary equipment, after unscrambling, the preforms are send the railway orderly. This railway allows the preforms are sendtto host blowing machines by self-gravity.
The preforms are caught and uploaded by rotary clamping hands to each heater heads, this movement is driven by mechanical cam in a soft and continuous way to make sure the high efficiency and the high stability.
Preform heating unit:
When it comes to bottling drinks production, 70% energy occurs at the blowing machine.
Lines are expected to continuously produce more with less. Besides maximize the capacity, it is also important to minimize the using cost.
We understand that every electricity watt you reduces can turn into massive return in the future.
Preforms are heated by lamps, in the heating box, the preform distance is controlled by 38mm only, which means more preforms are able to be heated by shorter heating box, compared with other blowing machine supplier, FG series blower only needs one heating box, and saves more than 50% than others.
In the heating zone, the preforms are not upside down, so no need puts extra robot hand to change its position before or after heating, also no-stop heating makes sure all preforms are heated evenly. This can give above 99.8% qualified rate of the bottles.
During heating, 5 fans are working together, by using the density of different temperature air to make sure the temperature of the heating section is constant. One Chimney is equipped; air pipeline can be connected directly to discharge residual air out of room. Below the preforms necks, there is equipped cooling water tunnel, this chilled water should be supplied by water chilled, it is to protect the preform necks not be heated and damaged.
Preform distance changing unit:
After heating, preforms caught by another robot hand to enlarge the distance of preforms, this enlarged distance will give proper space needed for blown bigger bottles. Robot hand is driven by servo motor only.
Blow molding section:
The robot hand then send preforms to blowing section. In this section we combine movements of bottom mold elevate, side mold camping, mold locking and up mold falling in one mechanical cam, this is the key. This design much simplifies the machine structure, all the movements are now controlled by mechanical cam instead of equipping many sensors, each mechanical movement has more logistical rules interlinked.
This cam is controlled by servo motor only. In this section, one water chilled will supply chilled water to give quick cooling for the mold.
After bottle blown up, they are caught by another robot hand to the conveyor which can be linked to the filling machine, this robot hand is driven by the same servo motor of the one who send preforms to the blowing station.
Until now, one recycle work of blowing bottles are finished
Mold Design and Process
(We offer bucket solution making sure bottle is good to blow and easy for downstream packaging industrial production)